What’s the difference between Case Hardening and Through Hardening?
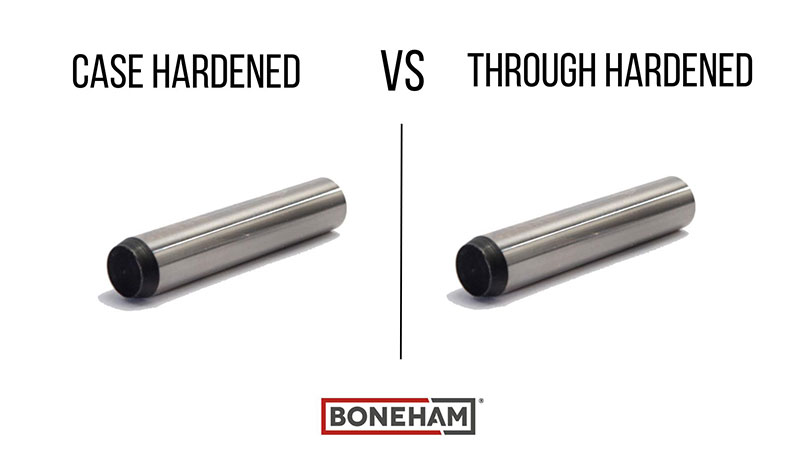
Case Hardening
Case hardening is the process of hardening the surface of a metal and tempering it back, while keeping the core soft and ductile. It’s used for steels with low carbon content (up to 0.7). Case hardening combines the benefits of hard and soft metal, giving you a component with the wear resistance of a hard metal and impact resistance of a softer metal, thanks to its yielding core.
Case hardened components are commonly used in applications with lots of friction. This includes Easy-Cone locator bushes and dowel pins in automotive or composite applications. The accurate ground outer diameter is resistant to wear, but the core remains resistant to horizontal forces.
Nitriding
Nitriding is a case hardening process that introduces nitrogen atoms to the steel component’s surface. It’s a more time-consuming, therefore costly process, that requires a specialist process and equipment, depending on the type of nitriding required, be it gas, salt bath or plasma.
However, nitriding creates a superior hardness on the surface of up to HRC 75, comparable to tungsten carbide. This makes nitriding an ideal alternative to carbide for high production drill bushes. The hard and even nitride layer can assist in the prevention of pitting corrosion in steels and increase the resistance of some 400 series stainless’s.
.jpg)
Carburising
Carburising adds carbon to the surface of a steel part to harden the surface. A carbon atmosphere is introduced to the furnace where the heat treatment is occurring. Then the component is quenched and tempered until the desired hardness is achieved. As this process introduces carbon to the component, any existing corrosion resistance in the metal is removed. Carburising stainless steel means it will stop being stainless.
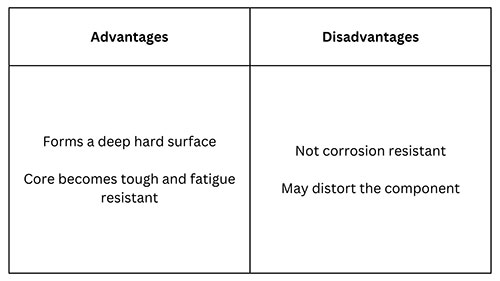
Through hardening
Through hardening (neutral hardening) uses a combination of heat, quench, and temper to significantly increase the hardness and improve the tensile strength of a steel. It ensures uniform hardness of the entire component, improves durability, and increases resistance to wear and heat.
Through hardened components are used in applications where hardness and wear resistance are needed. There are 3 steps to the through hardening process: Heating, Quenching, and Reheating/Tempering.
.jpg)
Heating
This step takes the metal above its critical temperature to modify the structural characteristics.
Quenching
Quenching rapidly cool the metal to achieve the desirable mechanical properties. Quenching is commonly done with oil or water. But some use liquid nitrogen, or air. The faster the quenching process, the more brittle the component can become.
For a more detailed insight, see this article by MSEstudent.com.
Reheating/Tempering
Tempering is used to reduce brittleness caused by the hardening process. The reheating restores ductility to make sure the component is usable and not overly fragile.
What's the difference between through hardening and case hardening?
The biggest difference between through hardening and case hardening is in the amount of the component that is hardened. As suggested by their names, through hardening hardens the entire component, whereas case hardening hardens the surface of a component and keeps the core softer and ductile.
If you need load bearing properties and wear resistance in your components, through hardened metal is more suitable. But if you require high strength and fracture resistance, opting for a case-hardened part will better meet your needs.
We have a range of case hardened and through hardened tooling components for engineering . For further assistance selecting the correct option for you, please contact our sales team with these details.