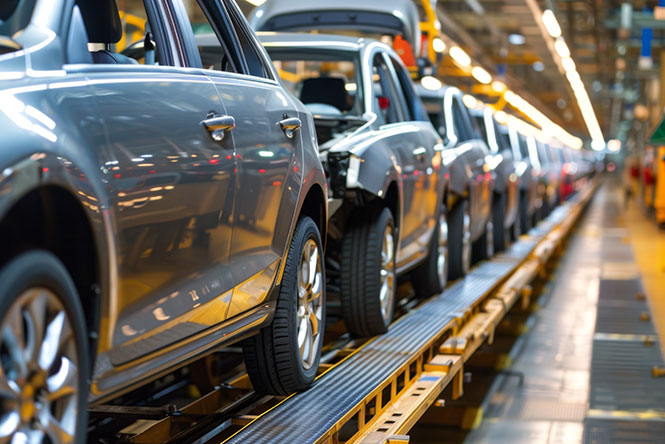
Automotive Solutions
Car manufacturers are increasingly dependent on a reliable and flexible supply chain. The adopted principles of just-in-time manufacturing mean supply chain service providers and manufacturers are required to support OEM’s in minimising waste and maximising operational efficiency.
How Boneham helps deliver automotive projects
Having served the automotive industry for over 100 years, we are an established and recognised supplier. Our customers benefit from accurate deliveries, reliable inventories, reactive machine capacity, and, above all, strict quality procedures. We work collaboratively with companies at all tiers of the automotive supply chain to create customer-centric solutions that exceed expectations while providing good value. With a UK manufacturing centre and partnerships across the globe, we are renowned for delivering quality and efficiency through all solutions.
Speed and Efficiency
Our large standard component inventories, and fast turnaround of tailored items have proven over many decades to help dynamic and successful automotive manufacturers take competitive advantage and pursue whole life reliability. Tailored or special parts can be stocked and released to order.
Quality Components
All Boneham components meet strict quality standards. With continuous investment in inspection equipment and adherence to our AS9100D (EN 9100:2018) and ISO9001:2015 QMS. As one of the leading suppliers of shims, dowel pins and location pins into automotive manufacturers and distributors in the UK, performance is always at the top of our mind. The Koenig range of sealing plugs and flow restrictors are trusted by the World’s leading automotive OEM’s, with zero defect and 100% inspection.
Flexibility
Dynamic industries may require special component sizes to suit unique designs and advancements in propulsion technology and sustainability. Our tailored commitment to Boneham components, ensures rapid response and turnaround on non-standard sizes, part marking, colouring or kitting. We work with our customers to manufacture tailored components to suit project lead times and category budgets.
Innovation
For many years, Boneham and Turner has used a collaboration method with customers to develop solutions for the future that help industries like automotive, to gain competitive advantage and reduce waste. Our engineers work to continually improve and develop both product and process to ensure rapid response, competitiveness and cost control.
Strong relationships
At the heart of the Boneham philosophy is relationships. We build long-term partnerships to ensure mutual growth and success. Developing components and services to ensure customer project realisation. The use of key account management facilitates smooth operations and issue resolution.
Sustainability
We work continually to progress down our journey of sustainability. Energy efficiency and waste reduction is a key driver in all new investment decisions and product development initiatives. After minimising waste, we ensure all possible waste segregation and recycling.
The Boneham Advantage
- 99.9% pick & quality accuracy
- Strict quality standards
- UK manufacture & low cost sourcing
- Large inventories
- Strong distributor and fulfilment relationships
The Boneham Automotive Story
Our Pedigree
During the period from 1921 to 1939, Boneham & Turner not only produced many thousands of reconditioned engines but also produced most of the components for the ERA racing engine. This included cylinder blocks, cylinder heads, crankcases, connecting rods and many other critical components. Further developments saw the company manufacture our own honing machines to create the cross-hatched finish required for optimum oil retention. The company was still working on the E.R.A engine through the late 1940’s, and then, subsequently, the 16-cylinder BRM engine under the Mays Project. During this time Boneham & Turner manufactured and distributed most of the component needs for B.R.Macross British motor industry members, including, and among many others, Austin, the Standard Motor Co, and High Duty Alloys.
Boneham & Turner’s initial involvement was the machining of the cylinder heads (four per engine), and importantly, the hemispherical combustion chambers. Using a S.I.P Jig Borer, specialist tooling and the standard Boneham & Turner BH6 Boring Head. This principle was adopted for a special fine boring machine for Jaguar Cars to machine the hemispherical combustion chambers on the aluminium cylinder head of the new XK engine that was being fitted to the XK 120 sports car and the Mark 7 saloon. The machine carried on through the engines production life. Later, in 1957, we supplied Humber with a similar machine for the Super Snipe engine.
In the 1970’s we became the UK distributor for Koenig components. Originally designed for high pressure hydraulic applications – Koenig expanders completely seal drilled holes. The reliability and efficiency of Koenig components saw them quickly adopted by OEM’s as they could be efficiently integrated into existing high volume production lines. We are the only supplier of SFC Koenig products in the UK. SFC Koenig expanders and check valves provide metal to metal sealing of drilled holes. Koenig Expanders seal holes with complete reliability and resist pressures of up to 500 bar. As a low waste sealing solution, Koenig Expanders have a massively reduced whole life cost compared to other component solutions, and they can help you reduce the carbon footprint of your production process.
BONEHAM products are manufactured in accordance with our ISO 9001 processes with significant onsite inspection and testing facilities. Certification is available and must be requested at time of order. Special labelling and batch numbers can also be requested on certain high volume products.